Ball Milling Technology: From Comminution to a Platform for Material Innovation
In a study published in Applied Catalysis B: Environmental, Tang and his team applied a high-throughput mechanochemistry strategy to uniformly anchor single-atom nickel (Ni) onto a g-C₃N₄ support. This approach significantly enhanced the activity and selectivity of the resulting photocatalyst for CO₂ reduction (CO₂RR).
To achieve this, the research team employed the PMQW2 omnidirectional planetary ball mill. Its unique 360° three-dimensional rotation enabled thorough mixing between the metal precursor and the support material, effectively promoting high dispersion and stable anchoring of the single-atom catalytic sites. This high-energy ball milling process not only replaced the traditional high-temperature calcination route but also greatly improved the synthesis efficiency and overall performance of the catalyst. The study highlights the enormous potential of mechanochemistry in sustainable material synthesis.
Reference:
Single-metal catalytic sites via high-throughput mechanochemistry enable selective and efficient CO₂ photoreduction
Applied Catalysis B: Environmental, 2022
https://www.sciencedirect.com/science/article/abs/pii/S0926337322006026
Three New Ball Mill Models Now Available from ANR

Designed for general powder grinding and sample pre-treatment, widely used in universities, R&D centers, and industrial labs.
- Supports both dry and wet grinding
- Multi-jar parallel grinding capability for higher throughput
- Final particle size can reach up to 0.1μm
- Various jar materials available (zirconia, stainless steel, agate, etc.)
PMQW Series Omnidirectional Planetary Ball Mill
Ideal for applications requiring excellent mixing uniformity, such as composites, electrode materials, and functional fillers.

- Unique 360° multi-directional rotation for thorough mixing
- Smart control system with data storage, programmable settings, and alarm features
- Widely used in MOFs, photocatalysts, battery materials, and more
HSVM High-Energy Vibratory Ball Mill
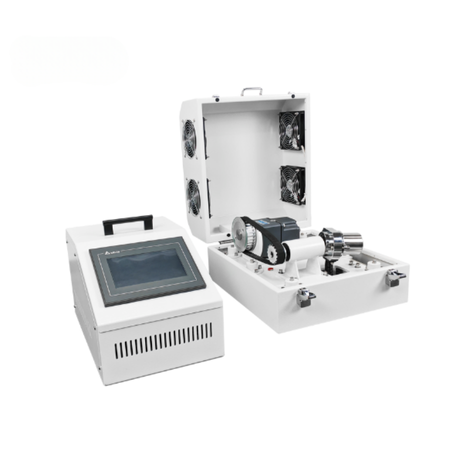
Tailored for high-energy, small-scale processing, especially suitable for nanomaterials, precious metal loading, and electrocatalyst development.
- Vibration frequency up to 1400 rpm
- Supports single or dual jar operation
- Capable of achieving sub-0.1μm particle sizes
- Multiple jar materials available for different systems
Application-Based Equipment Selection Guide

At ANR, we’ve supported many customers — including NTU, HKCU, and A*STAR — in selecting and setting up the most suitable ball milling systems for their unique research needs. Whether it’s for general grinding or high-energy reactions, there’s no one-size-fits-all solution. To help you navigate your options, here’s a quick guide based on common application types and the corresponding recommended models:
Application Type | Recommended Model | Key Features |
General powder grinding & pre-treatment | QM Series | High stability, universal usability |
Complex multi-phase material mixing | PMQW Series | Excellent mixing uniformity, programmable settings |
High-energy reactions / Nanomaterial synthesis | HSVM Series | High energy density, ideal for activation |
Let Rotation Spark Your Next Breakthrough
Ball milling technology has long surpassed its traditional role of physical grinding. It now serves as a crucial bridge between material design, energy transformation, and sustainable chemistry. Whether you’re working on batteries, electrocatalysis, nanomaterials, or photofunctional materials, choosing the right ball milling equipment can be the first step toward experimental success.
At ANR, we welcome your inquiries and are ready to provide detailed product manuals, model selection advice, and real research case support.
Other Blog Posts You Might Like
Company insight: How ANR helps our customers
Overcoming challenges in procuring laboratory products In the realm of scientific research, the procurement of…
Read moreOptimizing Research Efficiency with ANR’s Core Solutions
In material science research, efficiency is critical. Researchers are constantly managing experimental setups, conducting tests,…
Read moreEvent Recap: Future Development of Lithium-Ion Batteries – From ICAMEEH 2024
From September 24 to 27, 2024, we are honored to be the industrial exhibitor of…
Read more